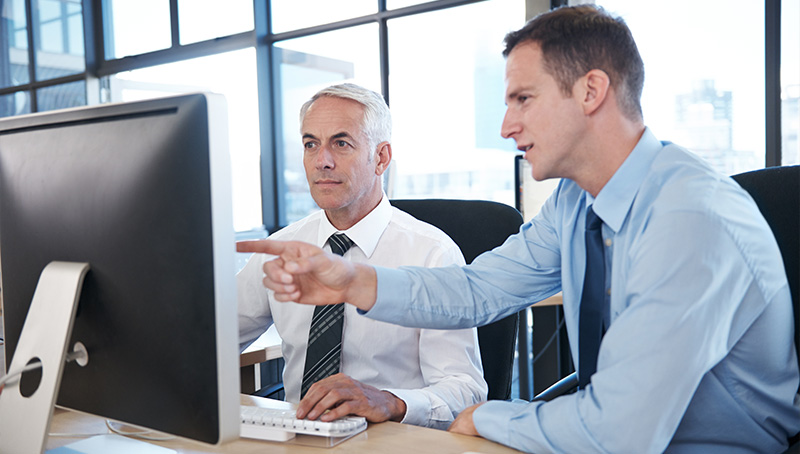
Effizientere Abläufe im Logistiklager
Operative Logistikprozesse profitabel steuern
Dass Ihr Lager schwarze Zahlen schreibt, hängt nicht allein von Strategie, Layout und Warenart ab. Diese Faktoren bilden vielmehr den Handlungsrahmen. Wie wirtschaftlich sie ihn nutzen, bestimmt zunächst einmal nur die Effizienz Ihrer Abläufe. Entscheidend ist daher das Zusammenspiel der operativen Prozesse. Wir zeigen Ihnen, wie Sie Ihre Prozesse optimal koordinieren. Und falls die Prozessänderungen dies erforderlich machen sollten, empfehlen wir Ihnen Anpassungen bei Layout und Strategie.
Inhalte
Zunächst untersuchen wir das Layout Ihres Lagers und die Struktur sämtlicher Abläufe – vom Eingang über Einlagerung, Kommissionierung, Auslagerung, Verpackung und Ausgang bis zu den Mehrwertdiensten. Schritt für Schritt ermitteln wir den Ist-Zustand inklusive der Prozesszeiten.
Aus der Ist-Aufnahme leiten wir prozessbezogene Kennzahlen für Ihr Lager ab. Deren Abgleich mit unseren Benchmarks zeigt, wo sich Optimierungen lohnen. Selbst Differenzen im Sekundenbereich sind interessant. In ihrer Gesamtheit bestimmen sie die Produktivität des gesamten Lagers.
Mit diesem Wissen erarbeiten wir konkrete Maßnahmen für ein Re-Design der Abläufe. Ihre Qualitäts- und Ergonomie-Ziele fließen mit ein. Ebenso die Vorgaben des Layouts und der Strategie. Nur das Zusammenspiel aller Faktoren führt zu wirklich nachhaltigen Produktivitätsgewinnen.
Beratung ist meist nur der erste Schritt. In der Regel setzen wir die Optimierungen mit unseren Kunden um. Auf Wunsch leiten wir das Change-Projekt und bringen alle Verantwortlichen an einen gemeinsamen Tisch.
Erreicht Ihre Performance die neuen Sollzeiten? Um täglich Bescheid zu wissen, geben wir Ihnen ein Controlling-Tool an die Hand. Anhand der aktuellen Auftragsstruktur ermitteln sie damit z.B. die Pickleistung je Stunde. Ergeben sich Abweichungen vom Soll, können Sie zeitnah reagieren.
Use Cases
Optionen für das Neukundengeschäft
Ist ein weiterer Hallenanbau sinnvoll? Mit dieser Frage kam ein Logistikzentrum auf uns zu, dessen Kapazität stets durch Anbauten gewachsen war. Unsere prozessgestützte Layout-Analyse machte jedoch klar, dass eine nochmalige Erweiterung die Profitabilität des gesamten Lagerbetriebs gefährdet hätte. Ungeachtet dessen ergaben sich für den mittelständischen Logistikdienstleister Handlungsoptionen auf einem ganz anderem Gebiet: Anhand unterschiedlicher Simulationen konnten wir ihm präzise aufzeigen, wo sich die Produktivität seiner bestehenden Prozessorganisation noch einmal signifikant steigern ließ. Der Weg führte vor allem über eine gezieltere Auftragssteuerung, welche die Komplexität der Lagerbewegungen zurückfuhr und die Synergien zwischen den Kunden ausnutzte.
Leistungen
In Einklang mit der Methodik ROTH gingen unsere Berater schrittweise vor. Hierzu gehörten folgende Teilschritte:
- die Aufnahme der Ist-Abläufe, inkl. der anfallenden Prozesszeiten,
- die Dokumentation des bestehenden Layouts in einem CAD-Modell,
- die Bewertung der Produktivität vor dem Hintergrund der kundenbezogenen Sendungsstruktur,
- unterschiedliche Simulationen zur Lagererweiterung, inklusive ihrer Auswirkungen auf die Prozessorganisation,
- ein verbessertes Regelwerk zur Steuerung der Lagerabläufe,
- die Definition lagerspezifischer Benchmarks, mit denen das Logistikzentrum seine Performance messen und bewerten kann.
Vorgehen und Nutzen in der Detailsicht
Ausgangslage
Zum Zeitpunkt unserer Prozessaufnahme diente das Multi-User Warehouse als überregionales Verteilzentrum für sechs Hersteller aus dem Konsumgüterbereich. Das breit gefächerte Warenspektrum reichte von Küchengeräten über Möbel bis zu Autoreifen. Hinzu kam ein Internethändler für Elektronikwaren. Jedem Kunden war ein eigener Bereich zugeordnet. Das Logistikzentrum setzte sich somit aus sechs voneinander abgegrenzten Lagerbereichen zusammen, die sich teilweise in unterschiedlichen Hallen befanden. Die Mehrzahl der Hallen verfügte über keine eigenen Tore.
Prozessaufnahme & Lagermodell
Unsere Produktivitätsberatung stützte sich auf zwei empirische Untersuchungen. Erstens auf die ganzheitliche Erfassung der Lagerabläufe, Prozesszeiten und bearbeiteten Sendungen. Und zweitens auf ein CAD-gestütztes Lagermodell, das die physischen Gegebenheiten aller Lagerbereiche sowie die anfallenden Weglängen detailliert wiedergab. Um diese Basisinformationen lückenlos für jede Schichtzeit zu erheben, waren wir fünf Tage lang mit drei Beratern vor Ort im Warehouse.
Verbesserungspotenziale
Quer über alle Kunden hinweg erwies sich die Komplexität der Wege als wesentlichster Produktivitätskiller. Insbesondere an Transporten zwischen den Hallen waren zu viele unterschiedliche Mitarbeiter beteiligt. Vor allem an den Übergabepunkten kam es regelmäßig zu Zeitverlusten. Neben solchen generellen Defiziten förderte die Produktivitätsanalyse zahlreiche kundenbezogene Prozessverbesserungsmöglichkeiten zutage. So etwa in der Verpackungssteuerung des Internethändlers, welche die eingehenden Aufträge vorwiegend in chronologischer Reihenfolge einlastete. Je nach Art und Größe der Ware führte dies allzu leicht zu Stausituationen oder Wartezeiten. Zudem wurden beim Kommissionieren Synergien verschenkt, die durch eine wegeoptimierte Kombination der unterschiedlichen Aufträge nutzbar gewesen wären.
Ergebnisse und Empfehlungen
Ausgangspunkt unseres Beratungsmandats war die Frage, ob die Errichtung eines weiteren Anbaus eine sinnvolle Option war, um zusätzliche Neukunden noch vom alten Standort aus zu unterstützen. Hierzu spielten wir im Hallenmodell diverse Layoutveränderungen durch. Keine dieser Varianten führte zu einem Business Case, der sich positiv gerechnet hätte. Hauptknackpunkt war der Umstand, dass der Anbau erneut ohne eigene Tore hätte auskommen müssen. Somit hätte sich die ohnehin schon bestehende Komplexität in den übrigen Hallen noch einmal so stark erhöht, dass die Produktivität des gesamten Logistik-zentrums in Gefahr geraten wäre. Vor dem Hintergrund dieser Ergebnisse sprachen wir uns eindeutig gegen eine Erweiterung aus. Unser Kunde folgte der Empfehlung und konzentrierte sein weiteres Neukundengeschäft auf einen alternativen Standort. Doch auch mit Blick auf das bestehende Warehouse ergaben die Simulationen eine Reihe von Möglichkeiten, um die vorhandene Hallenkapazität besser zu nutzen. Die erzielbaren Produktivitätsgewinne summierten sich auf eine bis zu 10 Prozent höhere Auslastung der Mitarbeiter. Den Löwenanteil an diesen Prozess-verbesserungen hatten drei Maßnahmenkomplexe: Erstens eine stärker kundenübergreifende Auftragssteuerung und –taktung, zweitens eine wege- und regal-höhenoptimierte Kommissionierung sowie drittens Veränderungen bei den Hilfsmitteln, die in der Kommissionierung und Verpackung zum Einsatz kamen.